Традиционный метод пошива лодок больше не стоит времени
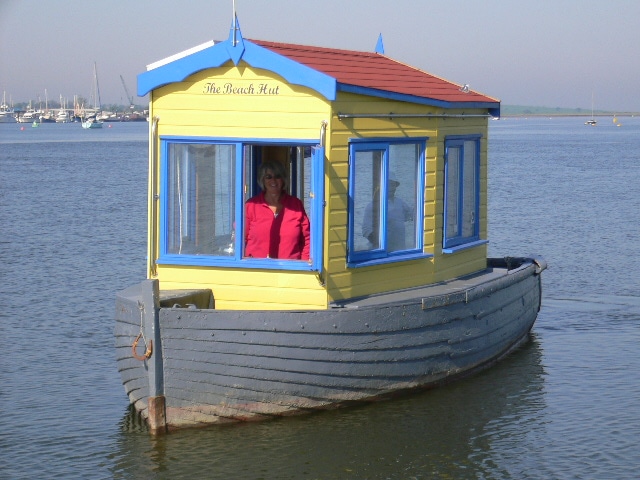
«Сектор производства лодок находится под огромным давлением, необязательно с целью постройки большего количества лодок, а с целью их более эффективного строительства, что позволит предложить более высокую стоимость или, что более важно, лучшую маржу, чтобы отрасль могла реинвестировать в свой персонал и оборудование», - пишет Дэвид Левин для Консультанты по глобальному морскому бизнесу поскольку он утверждает, что отрасль должна искать вдохновения в автомобильном секторе.
По словам Дэвида, слишком много лодок все еще строится традиционными методами «пошива».
«По-прежнему прилагаются огромные усилия (совершенно справедливо) для создания прочного корпуса с гладким гелькоутом, но часто с меньшим вниманием к внутренней части корпуса и фиксацией таких основных элементов, как переборки, в нужном месте - каждый раз, " он говорит.
«Переборки слишком часто обрезаются« зелеными »краями, чтобы их можно было разметить, а затем на них установить все остальное. Это означает, что лодку можно построить только линейным способом; одна часть сборки за другой - корпус, переборки и опоры, инженерия, мебель полов, палуба, облицовка подкрылка и т. д. Поскольку эти задачи в основном требуют разных навыков и времени выполнения, непроизводительные простои - это то место, где возрастают все расходы.
«Я видел множество лодок с расчетом стоимости каждой гайки, болта и единицы оборудования в Ведомости материалов, и даже справедливый удар по точным затратам на рабочую силу, но никогда не давал реалистичной количественной оценки времени простоя.
«Святой Грааль» должен заключаться в том, чтобы иметь дизайн - весь его - прямо перед началом производства; продумать все мелочи, например, где боковая облицовка встречается с подголовником или достаточно ли глубины и ширины в носовой части, чтобы создать подходящую кровать и т. д.
«Если все эти параметры могут быть соблюдены, то лодку можно будет строить« одновременно »- пока формируется корпус, можно планировать, заказывать инжиниринг и производить такие вещи, как электрический ткацкий станок. В то же время мебель может быть передана в деревообрабатывающий цех или на аутсорсинг, любая оснастка изготовлена, а мягкая мебель спланирована и запущена в производство ».
Дэвид очень хочет подчеркнуть, что нет замены времени проектирования на компьютере и построения полной виртуальной модели лодки. Для некоторых временные затраты могут показаться возмутительными, но здесь нет материалов, которые были бы неправильно или расточительно вырезаны, нет времени, затрачиваемого на снятие фаски или подгонки деталей на место, и нет простоев в ожидании доставки или изготовления деталей. И лодка наконец будет собрана гораздо быстрее.
«Многие компании во многих странах приняли это сейчас, - продолжает Дэвид, - но меня все еще беспокоит то, что многие более мелкие компании в Великобритании, используя ту или иную форму САПР, не доводят ее до конца, обычно потому, что не уверены, что именно они хотят, и решат, когда это будет на месте.
«Это ничем не отличается от того, что потенциальный владелец просит изменить спецификацию во время постройки лодки, за что вы бы взяли много денег - только на этот раз это стоит больших денег из-за еще большего времени простоя, пока принимаются во внимание решения и сроки выполнения заказа.
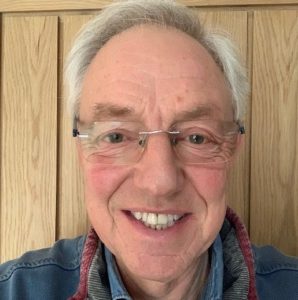
«Это небольшие компании, которые в основном не имеют ресурсов, чтобы справиться с трудностями в строительстве, и поэтому больше всего выиграют, работая над полным пакетом дизайна, прежде чем переходить на стекловолокно, смолу и дерево. Не торопитесь с дизайном и с первого раза соберите лодку правильно - и в рамках бюджета ».
Дэвид является частью недавно созданной группы Global Marine Business Advisors, группы профессионалов мировой морской индустрии, которые объединились, чтобы предложить свои знания и услуги по отдельности или коллективно мировой судоходной индустрии. Читать его статья полностью.